Ever since designed by Takeshi Nii from Japan in 1970, Nychair X has been prized as a masterpiece chair across more than 50 countries around the world. The simple, elegant, and functional design befit for any occasion is rooted in Japanese dwelling and cultural heritage. Still today, the chair is appreciated and cherished by users around the world for the quality uniquely imparted in Japan to deliver ultimate sitting comfort.As the time-tested tool crafted for better living, Nychair X will continue to deliver ultimate sitting comfort to users around the world with quality uniquely imparted in Japan.
Seat fabric
Durable and thick fabric to support your body.In order to maintain the strength necessary to comfortably support body weight when seated, the seat is made using twill weaving technique, the same as used in denim. To recreate the Nii’s idea of “softness as if it was washed once”, the fabric’s surface undergoes a process where it is scratched to make it fluffier. Usually, the dyeing and water-repellent finishing are done at the same time after weaving, but our process is different: after dyeing, the fabric first undergoes the fluffing process, and then a water-repellent finishing is applied.Takeshi Nii, being a third-generation owner of a company manufacturing kendo equipment, developed this unique seat fabric with inspiration from kendo uniforms and equipment bags. It is said he soaked the fabric in water and checked the tension with his feet. Currently, production is divided between two factories: one in Kurashiki, Okayama prefecture, and another in Takashima, Shiga prefecture. The weaving, processing, and dyeing are supported by a technological insight of multiple workshops to manufacture the final fabric.
Armrests
Natural and reliable material for parts that touch the body.Wood was used for armrests – the parts that are the most frequently touched – from the beginning, stemming from the thought that “natural materials are better because they make you feel relieved”. The structure of a human arm was taken into consideration to design armrests that prevent fatigue.Armrests are attached by only two screws, so even a small error in hole positioning might affect the angle of the frame and have a huge impact on the level of comfort. After trial and error, we have introduced a computer-controlled dedicated processing machine for Nychair X. Because the machine does everything from shaping the wood to making holes in the armrest, it has improved cost-efficiency, production volume, and precision.There are different colors used across the different product series, but in light-colored Natural and Soap Finish armrests, the wood grain and knots are highly visible, so to ensure the color and shades are coordinated in both armrests, final control is performed with human eyes.
Seat Pipes
In Nychair X seat is connected to the armrests by one type of screw in four places, which requires precise calculations to ensure the placement of the screws is aligned.Previously used cutting drills were replaced with lasers to prevent difficulties with assembly. The change made it possible to eliminate subtle position changes during processing and residue inside and outside the pipe, which were the reason for problems when threading the screws.
Leg Pipes
Advancement in bending technology, focus on beautyThe pipes are formed by folding a stainless steel sheet into a tubular shape and welding the connecting ends together. To prevent spoiling the beauty of the legs, the inside of the hole is inspected, and the processing is done after making sure the welding marks are facing the inside.The pipes are finished with a hairline matte surface to prevent excess shine and allow the chair to blend with an interior better. Additionally, it also helps conceal any scratches on the pipes that might develop during continuous usage. There is no need for maintenance, such as repairs or coating, and the chair can be loved for many years while retaining its beauty.
Screws
To avoid breakage due to deterioration and prevent rust, which can make a screw unmovable, we have used stainless steel in new generation model instead of regular steel.Since it was first released, NychairX has been made to be easy to assemble and disassemble; only cross-head screws are used, allowing assembly with a single Phillips screwdriver, which can be found in almost any household. However, because the screws connecting the two leg pipes were prone to loosening over time, we have used screws that tighten more firmly for elements not requiring assembly.Nychair X 80 has many moving parts, and compared to Nychair X, the screws are more vulnerable to loosening due to the chair's construction. To address this issue, the screws are coated with a special lubricant, which makes it harder to loosen them.
Efforts towards sustainable manufacturing
Getting things we become attached to and continuing to use them for a long time not only enriches our everyday lives, but also contributes to reducing waste and the burden placed on the environment by the production processes. To allow Nychair X to be enjoyed for longer by repairing any damages made during continuous use, we will be introducing additional replacement parts in our store. Please contact us for more information.We are trying our best to allow everyone to enjoy Nychair X as "a tool for good living that will always be loved" over the generations, passed from parent to child, from child to grandchild.
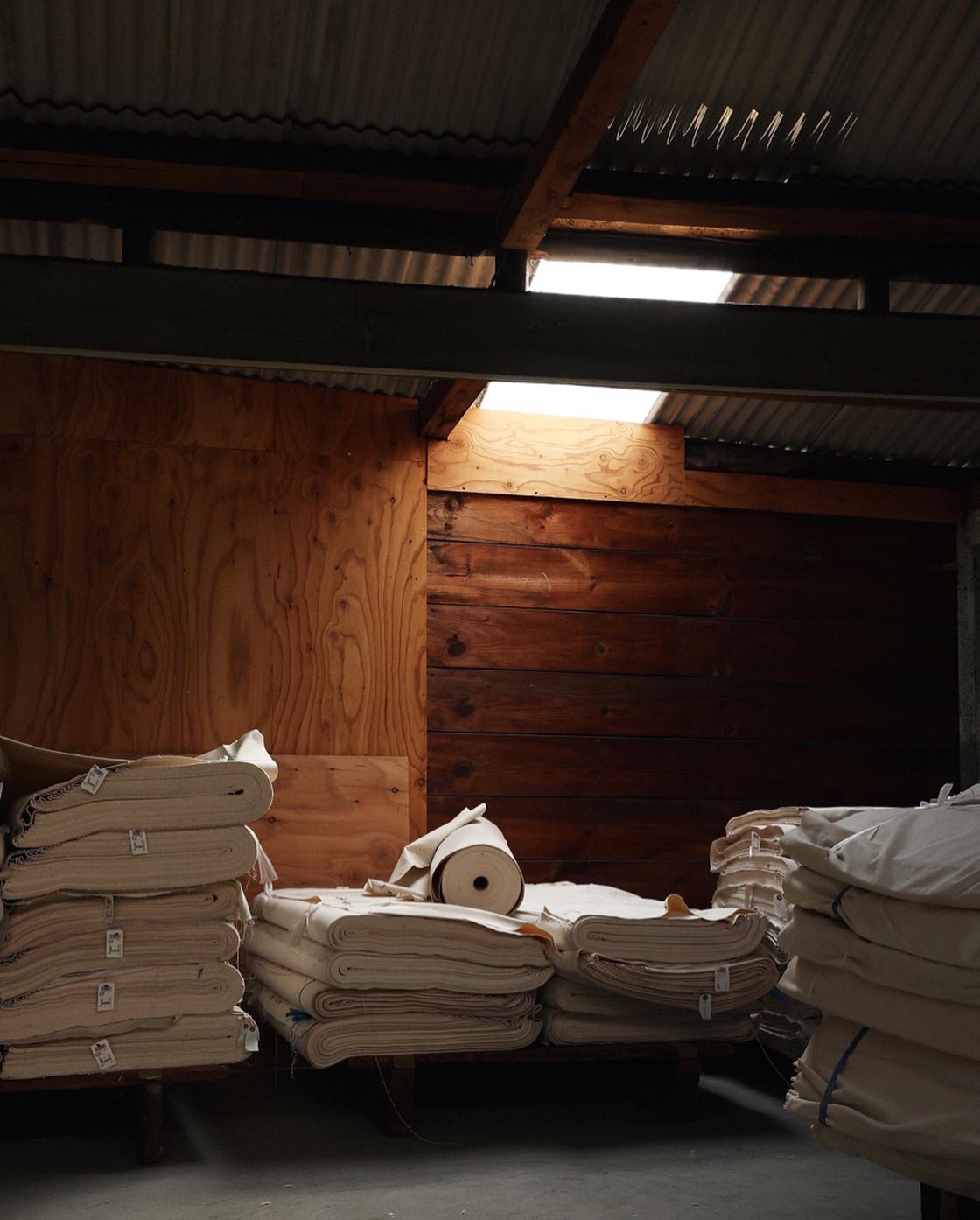




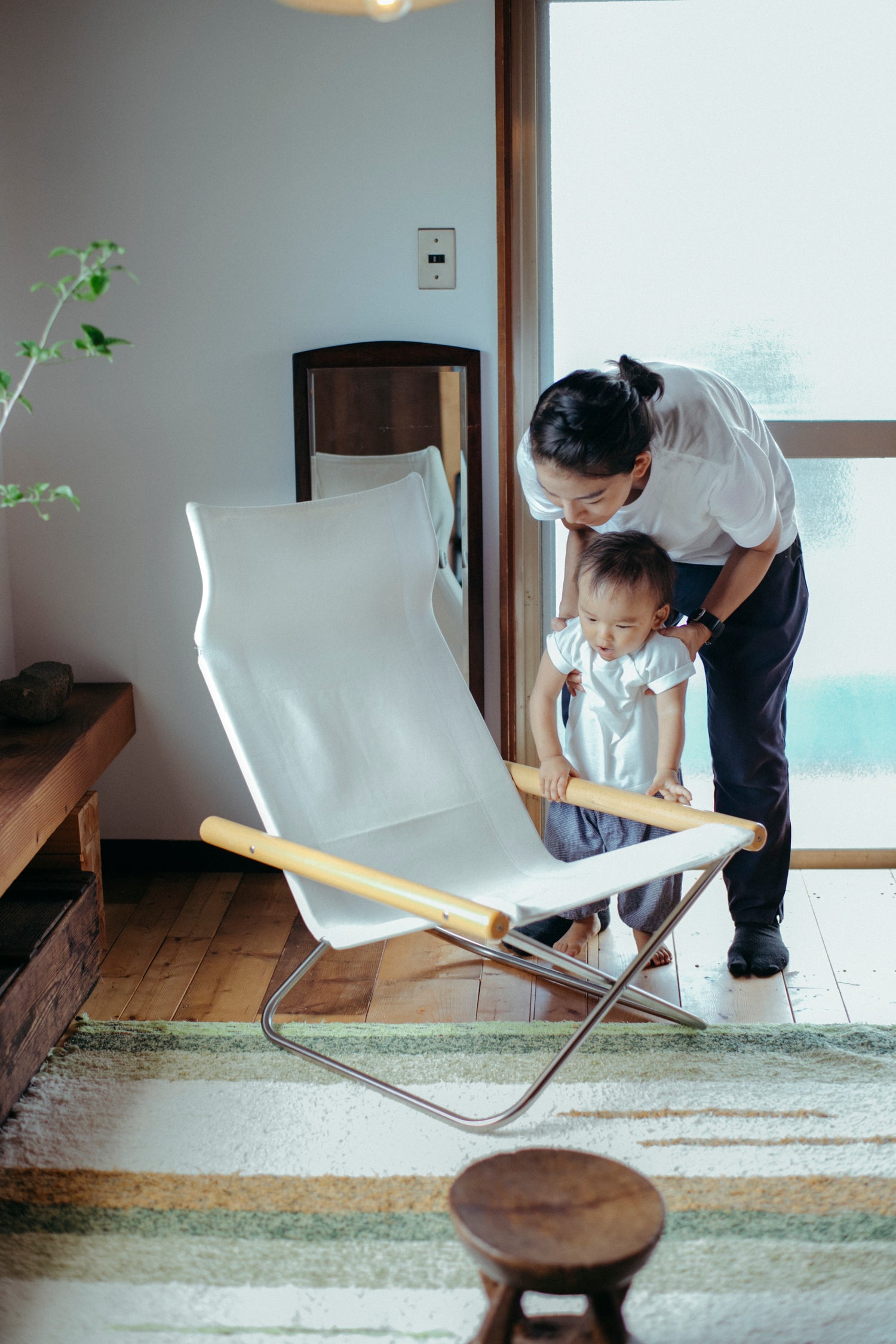